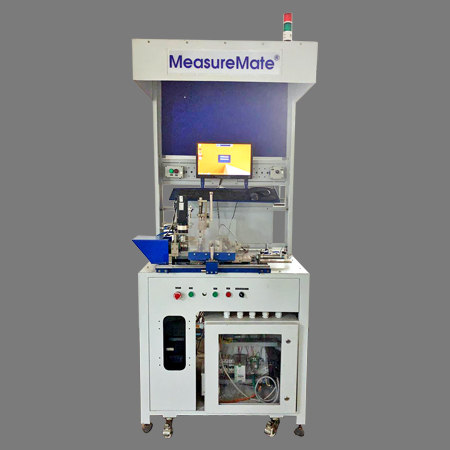
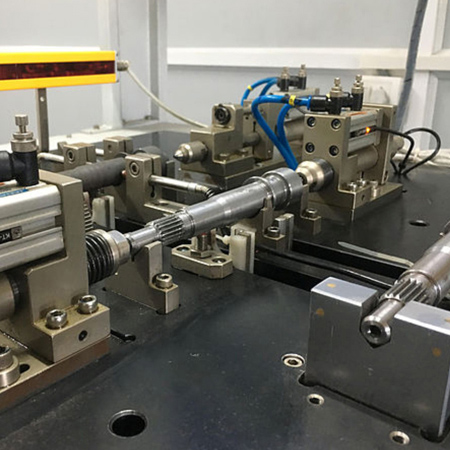
Applications and benefits
Mult-gauging
Benefits
Manual v/s MeasureMate
Mult-gauging
Gauging Machineg with 100% quantified inspection
MeasureMate is Industry’s most innovative multi-gauging solution for for gear profile measurement, transmission shaft, Gear Shaping Machines, EV gears, internal gear measuring inspection with a centralized data management system. The machine is designed to bring rejections down to near zero for original equipment manufacturers and their vendors. It simplifies the inward inspection process, eliminates stoppage due to rejection of components, and drastically reduces the possibility of faulty parts going to the customers.
Benefits
Computarised Data(within 2µ).
100% traceability.
Data Measurement
Real-time inputs to process correction (Cp/CpK).
One stop solution
Single platform for all measurements.
Remote monitoring
Automatic and instant PDI Report.
High accuracy (within 2µ)
100% recording of all measurements.
Manual v/s MeasureMate
Manual Gauging Machine – MeasureMate
- High manpower for inspection of ID, OD, PCD Runout, DOB, Groove width, spline inspection parameters etc
- High space & Manpower required for 100% inspection of multiple parameters before dispatch..
- Human errors adds up to internal rejection- Mixing of OK & Not OK components.
- Dependency on skilled manpower
- No data for traceability or analysis
- Calibration frequency is not always ensured results in rejection skipping to customer.
- Poor R & R of manual equipments
- It can’t be integrated to scanner/dynamic marking.
- Manual equipments will be obsolete in future
- Critical to measure parameters are sometimes impossible to measure on manual equipments.
Gauging Machine MeasureMate® Benefits
- Unskilled operator can achieve 100% inspection on MeasureMate™.
- 100% inspection of all the CTQ parameters on one MeasureMate™ occupying optimum space.
- MeasureMate™ makes the operator keep Ok & Not ok components separately (Pokayoke)
- All the data required for SPC analysis is recorded & can be transferred to remote PC.
- Calibration frequency is ensured by MeasureMate™.
- Great repeatability of MeasureMate.
- MeasureMate™ saves inspection results against scanned QR/ bar code and does dynamic marking.
- MeasureMate™ is future ready, Industry 4.0 ready. Can be upgraded for new components, software &Industry 4.0 features
- Critical to measure parameters like ball track diameter and it’s runout, Runouts w.r.t. two datums etc can be automated.
Watch video
Gauging Machine - CTQ Parameters
- Span measurement (attribute/ quantified type)
- Diameter Over Ball (DOB/MOT) (attribute/quantified type)
- Center distance
- PCD runout of splines/ gear
- Internal Diameter
- Outer Diameter
- Face runout & various other runouts
- Lengths
- Groove width & groove distance
- Diameter Under Ball (DUB)
- TCE/TTE of internal gears
Shift to most advance way of gear inspection
Setting process made so easy that unskilled operator can do it
Case Study
Automation ensures zero PPM rejection in internal gear inspection
Blog
Build an impeccable process to avoid losses
Learning by sharing
Auto Gear Roll Tester to inspect 5 parameters and 9 variants
Inspection of Gear by checking 16 parameters on 4 variants in
Gear Rolling Tester – Operator conducted two tests simultaneously single-handedly. Labour-dependent
Gear inspection method for automation Your gears are examined meticulously in