A Spline Yoke manufacturer faced an inspection process that needed too much
manpower, took up excessive space, and relied on manual data tracking. With
MeasureMate’s automated solution, they turned it around reducing operator
dependency, saving space, and achieving reliable, traceable data.
Best of all, they boosted Spline Yoke inspection capacity by 20%!
The Spline Yoke Inspection process had several challenges but MeasureMate addressed them all
Pain
Gain
17 operators needed for inspections
3 operators required with MeasureMate
1,000 components inspected per shift
1,200 components inspected per shift
Large space required to house multiple gauges
Significantly lower space as all gauges
integrated into a single MeasureMate
Manual data recording dependent on
operator skills
Automated data recording, zero errors with
MeasureMate
The Results
82% Reduction
in Manpower
20% Increase in Inspection Capacity
100% Traceability
and Accuracy
100% Reduction
in Operator Dependency
Long-Term Benefits
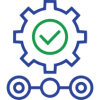
faster throughput
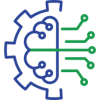
compact system
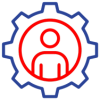
Manpower optimization
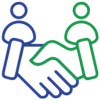