A renowned Gear manufacturer struggled with operator dependency in their inspection process.
Their inspection of critical shafts across 16 different parameters required skilled operators to
manually set up and run multiple gauges..
The Gear Manufacturer was looking for an efficient way to handle
complex inspections with minimal operator involvement
The process had several challenges but GearMate Superior addressed them all
Pain
Gain
Inspection & Dispatch bottlenecks when skilled
workers were unavailable
Reduced operator dependency, ensuring
continuous production and inspection flow
16 high-precision parameters (TCE, TTE, Fr, etc.)
needed to be measured down to 0.008mm
across different gauges
All 16 parameters measured accurately in one
integrated system, ensuring 100% okay parts
are dispatched.
Lengthy setup times and frequent
recalibration for different gauges to measure
parameters
Setup time reduced from 1+ hour to 15
minutes, eliminating the need for manual
recalibration
Inconsistent manual measurements, leading
to errors and rejected parts or obsolete of
parts
Real-time feedback with 100% accuracy,
minimizing errors and rejections
Results
100% Accuracy
in Inspections
75% Faster
Setup Time
Zero rejection after dispatch leading to
Growth in Customer Orders
100% Reduction
in Operator Dependency
Long-Term Benefits
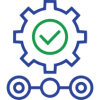
Increased Productivity
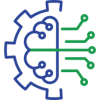
Simplified Operations
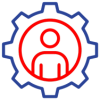
Eliminate Operator Dependency
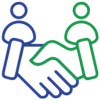